
Corrosion Engineering
Atmospheric corrosion, aqueous both in static and dynamic fluid conditions and high temperature corrosion research are the central theme of the group. The research is strongly driven by the corrosion problems encountered by the industries. The atmospheric corrosion to study the local environmental impacts including polluting gases as well and suspended particle on the materials performance has been established.
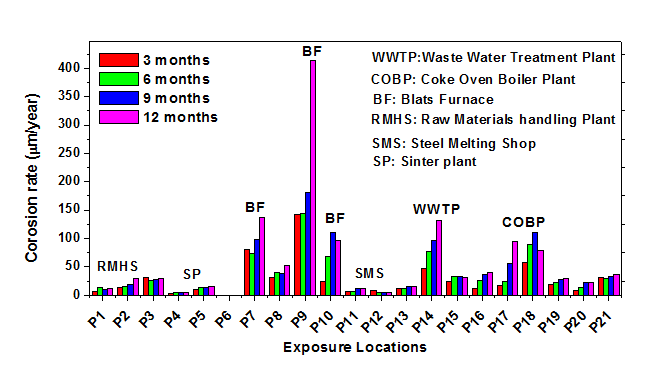
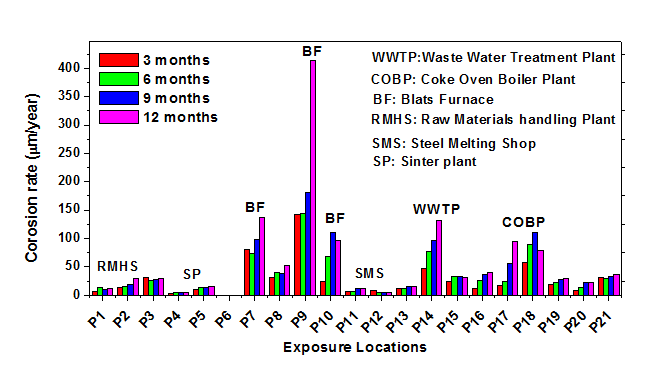
Increasing industrialisation or shift in the regional or global climatic conditions has not only been challenging the lives but materials too. The study performed in the recent past and present by this group on the corrosivity of different environments or corrosion resistance of various engineering/ structural materials across the country has been established.
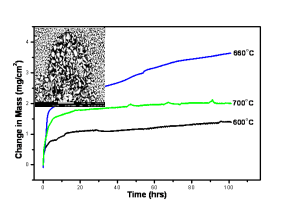
The material degradation at high temperatures relevant to futuristic ultra supercritical boiler environment is priority area of research. High rate wastage due to hot corrosion and oxidation at boiler temperature~ 760oC inflicts sever materials limit. High chromium containing or nickel alloys appear candidate for such corrosive condition. The mechanism of their failure and sustainability needs to be established in situation of adopting new boiler technology for minimizing the carbon emission from power plants.
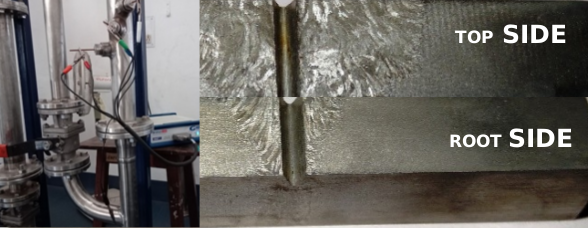

Flow assisted corrosion relevant to various industrial processes remains a concern. The research is also actively being pursued primarily in the synthetic sea water with varied oxygen concentrations at different flow speed. The operational, in addition to material’s, parameters such as corrosive anions, oxygen, and hydrodynamic, play key role in erosion and localised corrosion of line pipe steel. The stainless steel pipeline related to nuclear and chemical industries undergo severe intergranular corrosion, often induced by the low temperature sensitization either during exposure to fabrication or process temperature. Predicting long term integrity of stainless steels against IGC induced failures are challenging.
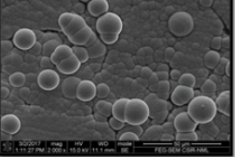
The application of magnesium alloys due to high specific strength to weight ratio is though growing, their poor corrosion resistance is the biggest limitation. The coating magnesium alloy to extend their useful service life using aqueous or non-aqueous solvent is extremely difficult due to exceedingly high corrosion rate. This needs special pre-treatments which of another focus of our studies.
![]() | ![]() |