About CSIR-NML
Profile
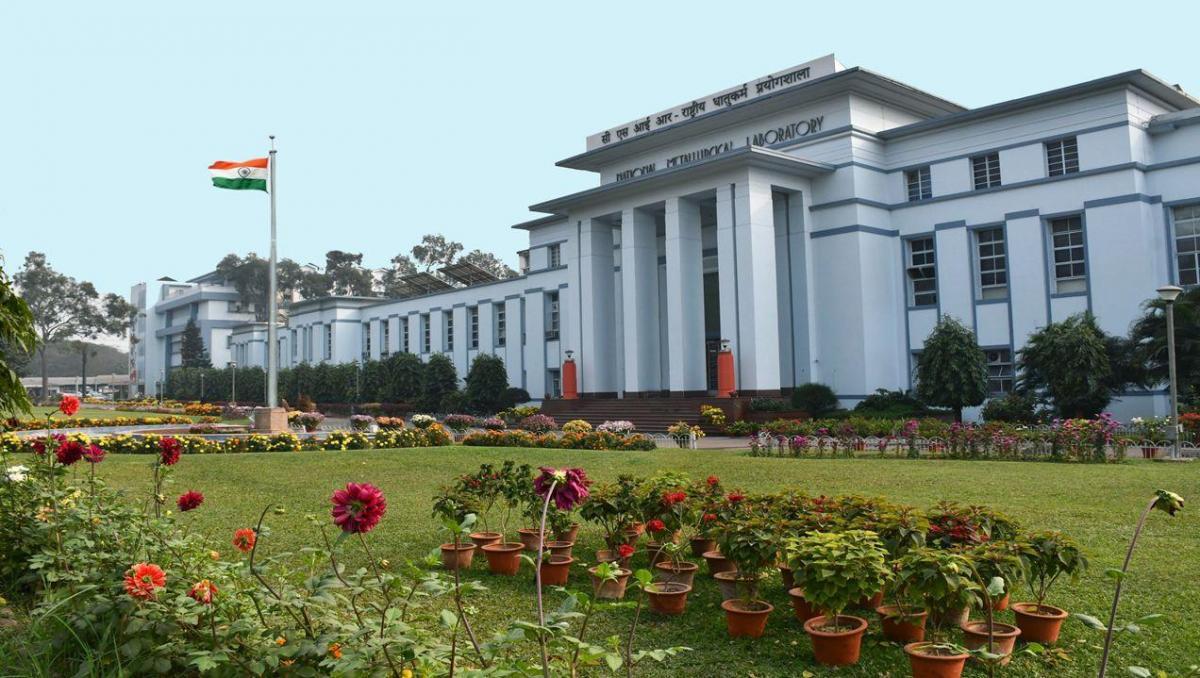
The CSIR-National Metallurgical Laboratory (CSIR-NML) is a leading metallurgical research institution in India, located in Jamshedpur. It has emerged as one of the global leaders in minerals, metallurgy and materials research back-up by substantial share of research publications in peer-reviewed journals and intellectual property products generated in metallurgical and materials science and technology. The foundation stone for CSIR-NML was laid by Honourable Sri C. Rajagopalachari on November 21, 1946. It was formally inaugurated and dedicated to the nation on November 26, 1950 by Pandit Jawaharlal Nehru in a spirit of hope and in a spirit of faith in the future. CSIR-NML research activities are aligned with national priorities like "Make in India“, "Innovate in India“, and sustainable development goals. CSIR-NML collaborates with industries and other research organizations to translate its research findings into practical applications.
Mission
To develop technologies that meet the need of the country, provide sustainable solutions to Industry and add value to our society through dissemination of knowledge, skill building and developing entrepreneurship.
Vision
To be a nationally relevant, globally benchmarked and self-sustained technology & innovation centre in Minerals, Metals and Materials Engineering.